DBF-120 Discontinuous Block Foaming Machine: Low-Cost Innovation for Emerging Foam Manufacturers
- Omar Moujaes
- Jan 13
- 3 min read
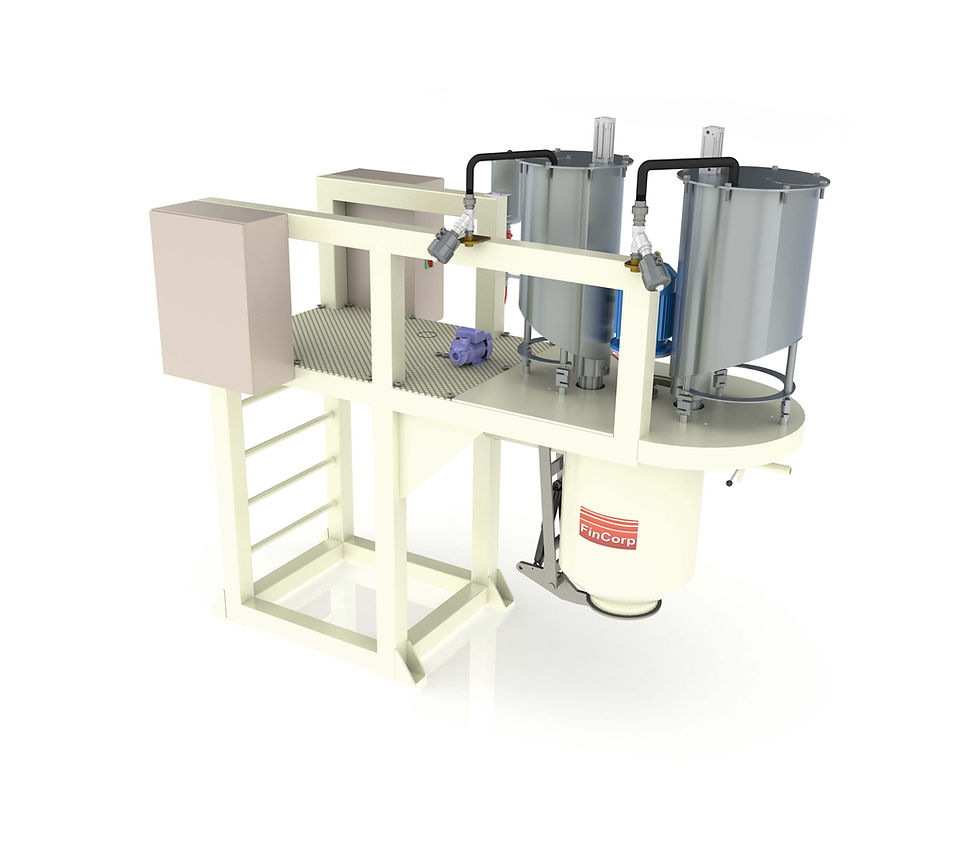
A Brief History of Discontinuous Block Foaming and the DBF-120 Machine
Foam has been a staple in the furniture, bedding, and insulation industries for decades, and for good reason—it’s lightweight, versatile, and can be tailored to a range of densities. But producing foam blocks used to require substantial investments in complex machinery, making it a challenge for small and emerging markets. That’s where the idea of developing a cost-effective, semi-automated block foaming machine began to take shape.
Back in 2003, as part of the push to phase out ozone-depleting substances like Freon under the Montreal Protocol, there was growing demand for a cleaner substitute—methylene chloride. FinCorp recognized this shift as an opportunity to help developing-world foam manufacturers adapt. Through a series of contracts with the UN, FinCorp embarked on creating an accessible yet advanced solution: the Discontinuous Block Foaming Machine, or DBF-120.
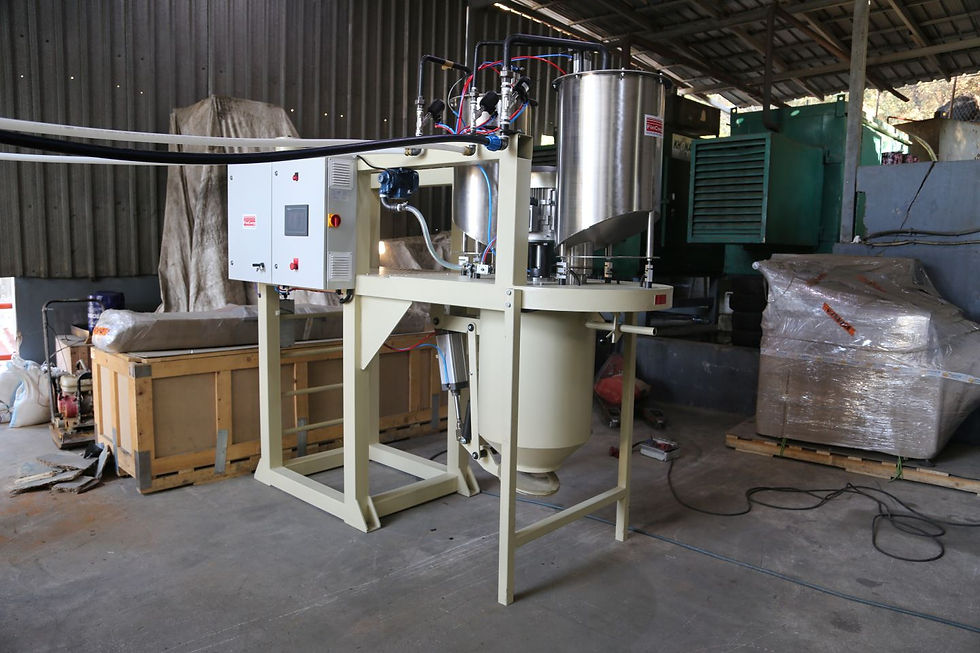
Why Discontinuous Block Foaming?
The principle behind discontinuous block foaming is straightforward but powerful. Chemical ingredients such as Polyol, TDI, Amine, Silicone, Water, Tin, and (when needed) Methylene Chloride are precisely mixed and dispensed into a rectangular block mold. As these components react, the mixture expands into a resilient foam block, perfectly matching the mold’s dimensions. This process is particularly beneficial for manufacturers in developing regions because it balances low capital expenditure with high production quality.
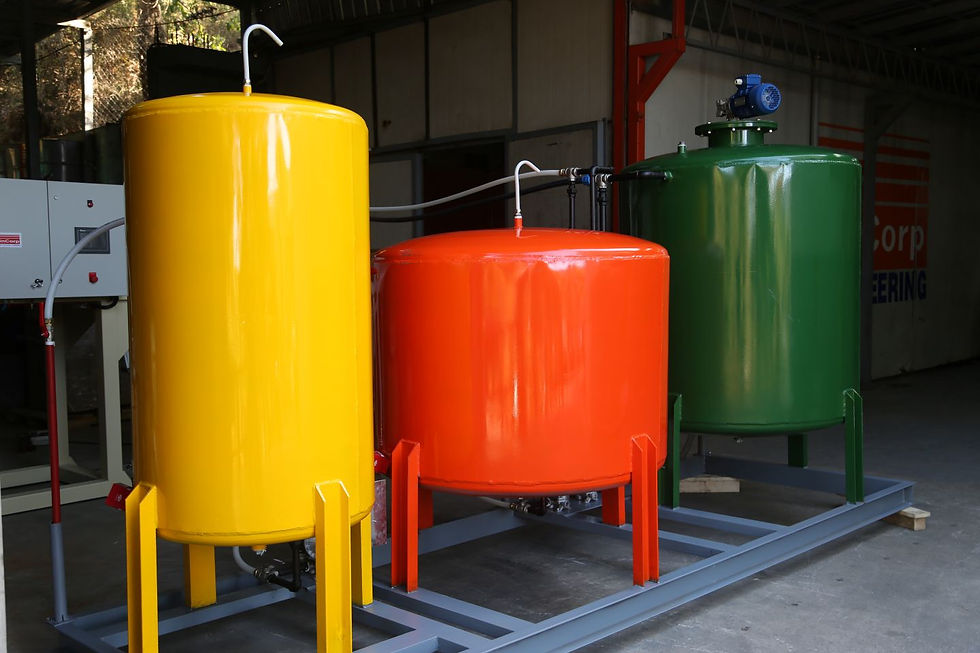
The DBF-120 Machine refines the foam production process with an emphasis on:
Simplicity: The control system, with an intuitive touch screen interface, makes operation straightforward even for new users.
Accuracy: A dual weigh system ensures exact measurements, crucial for achieving consistent foam densities up to 80 kg/m³.
Reliability: By utilizing reputable components—Festo pneumatics (Germany), Schneider electric (France), Omal valves (Italy), and Delta controls (Taiwan)—the DBF-120 is built to last.
Flexibility: Whether you’re producing flexible polyurethane foam for mattresses or high-resilience foam for specialized furniture, this machine handles a wide range of densities.

Key Advantages for Emerging Markets
Low Cost, Low Installation Hassle
The DBF-120’s design prioritizes minimal upfront investment. Its compact footprint and simplified setup mean you don’t have to completely restructure your facility to get started.
Efficient Chemical Usage
Accurate pumps and a weight-based control system guarantee you’re using the right amount of each ingredient—no more, no less. This efficiency can significantly reduce production costs over time.
User-Friendly Operation
With clear controls and easy-to-learn procedures, your team can quickly adapt to the system. Minimal training means you can ramp up production without long onboarding periods.
Versatile Production
From flexible foam for furniture to memory foam for bedding, the DBF-120 accommodates a wide variety of foam types. It’s a one-stop solution for both newcomers and seasoned foam producers.
Quality Components for Longevity
By sourcing high-quality European and Asian parts, FinCorp ensures that the DBF-120 continues running smoothly even under demanding conditions, offering a long machine lifespan.

A Complete Package, Ready to Go
The basic DBF-120 model comes with a 120-liter (150 kg) capacity, a user-friendly weight system, and computer controls—all standard. It also includes a water flush system and an air pump filling mechanism, offering everything you need to begin production the moment it arrives. Molds can be customized to various sizes, enabling you to produce foam blocks that suit your exact requirements.
Looking Ahead
Since its inception, the DBF-120 Discontinuous Block Foaming Machine has played a vital role in helping early-entry companies thrive in the foam industry. By offering a high-quality product at a lower capital cost, FinCorp Engineering continues to support developing regions in meeting global environmental standards—while still producing top-tier foam products.
Whether you’re a small-scale startup exploring foam production for the first time or an established manufacturer looking to expand capacity, the DBF-120 proves that advanced foam manufacturing doesn’t have to be prohibitively expensive or complex. It’s all about striking that perfect balance between cost, quality, and reliability—something this machine has been doing since its origin in 2003.
Interested in learning more about the DBF-120 or foam production in general? Keep exploring our blog for in-depth guides, tips on maintenance, and industry updates that matter to foam producers around the world.
Comments